- 과학향기 Story
- 스토리
스토리
조선낫, 최고의 명품으로 거듭나다
<KISTI의 과학향기> 제362호 2005년 11월 02일
조선낫이라고 있다.
불과 10여년 전만 하더라도 조선낫은 벌초를 갈 때면 빠뜨릴 수 없는 연장이었다. 숫돌에 시퍼렇게 날을 간 다음 행여나 다칠세라 새끼줄로 칭칭 동여 맨 뒤 조상님들의 산소를 향해 떠났는데, 낫 한 자루면 모든 것이 해결 가능했다. 풀은 말할 것도 없고 두꺼운 식물이나 작은 나뭇가지도 거침없이 쳐낼 수 있었던 것이다. 기특한 것은 굵고 단단한 나무를 베거나 쳐낼 때 날이 닳아지기는 하더라도 부러지거나 이가 빠지지는 않는다는 것이다.
이런 낫을 만들어 내는 모습도 볼 만했다.
‘싼 값’을 무기로 공장에서 대량으로 찍어내는(주조방식) 왜낫과 달리, 조선낫은 대장간에서 대장장이가 직접 두드려(단조방식) 만들었다. 화덕에서 꺼낸 시뻘건 쇳덩이를 두드리고 물에 담그는 순간 치지직∼쉬이익 소리를 내며 자지러지는 것을 다시 건져내 흥건히 땀방울을 적시면서 쇠망치로 수 백번을 두드리는 대장장이의 손놀림 끝에 조선낫이 탄생한 것이다. 그런데 대장장이들은 단순히 벌겋게 단 쇳덩이를 찬물에 담궈 급랭(急冷)시키고 두드리기만 한 것은 아니었다. 고온에서 급랭하는 담금질을 통해, 보통이면 일어날 변화를 일부 또는 전부 차단하여 필요한 특성만을 나타내게 한 후에는 비교적 저온에서 가열함으로써 담금질로 막았던 변화를 약간 진행시켜 알맞은 특성을 갖게 만드는 ‘뜨임’을 하고, 또 이를 천천히 식힘으로써 금속재료의 뒤틀림을 바로잡거나 상의 변화를 충분히 끝나게 하여 안정상태로 만드는 ‘풀림’ 등을 거치면서 쇳덩이의 성격을 완전히 바꿨다. 이 과정에서 조직을 보다 안정적이고 단단하게 만들기 위해 망치로 쇠를 두드려 주는 것이었다. 도대체 벌겋게 단 쇳덩이를 물에 담그고 두드리면 어떤 변화가 일어나는 것인가?
쇳덩이를 현미경으로 자세히 확대해서 보면 치밀한 금속 조직을 볼 수 있다.
네모, 육각형, 오각형… 모양만 다양한 게 아니라 크기도 제각각인데, 이런 조직들은 온도에 따라 조금씩 다른 특성을 나타내게 된다. 쇳덩이를 급랭시키면 냉각액과 접촉되는 강철의 표면조직은 단단한 마텐자이트가 되고 강철의 내부로 들어갈수록 냉각속도가 늦어져 조직은 질기면서 충격 흡수를 잘하는 펄라이트 조직으로 바뀌게 되는 것이다.
대장장이들은 이처럼 쇳덩이의 성질이 달라진다는 것을 날과 등의 두께를 달리함으로써 경험적으로 알고 있었다. 그들은 쇠의 색깔이 황혼 빛에 이르는 순간을 포착해, 안쪽 날부터 시작해 등 부분까지 순간적으로 물에 담그는 것을 반복했다. 날 부분은 갑작스레 담금질하면 갈라질 수 있기 때문에 손끝에서 나오는 숙련된 기술이 필수적이었다. 이런 과정을 수백 번에 걸쳐 반복하면서, 날 부분은 강하게 만들고 가운데와 등 부분은 약하지만 유연하게 만들었다. 조선낫은 이런 과정을 거쳐 단단한 ‘날’과 낫 날에 가해지는 충격을 흡수하는 ‘등’으로 만들어 졌던 것이다.
오늘날 단조방식으로 금속을 가공하는 원리는 우리 조상들이 사용하는 방식 그대로다.
바이트 ·드릴 ·끌 ·다이스 등 다른 금속재료를 자르거나 깎는 공구의 재료로 쓰이는 강철은 대부분 마텐자이트 조직이 되도록 열처리된다. 자동차 강판이나 항공기 부품 등에는 베이나이트 특성을 갖도록 가공한다. 다만 현대에 와서 달라진 것이라면 대장간에서 쇠를 두드려서 각종 도구들을 만드는 대신, 다이(Die)라고 불리는 아주 단단한 틀 위에 재료를 놓고 자동으로 두드리도록 하는 것이다. 또 급랭할 때 물 대신 기름이나 액체공기 속에 넣는 일도 있고, 찬 공기나 그 밖의 가스를 뿜는 경우도 있다.
그런데 아쉬움이 있다면 현재의 우리 기술수준이 조선낫을 만들던 대장장이의 장인 정신을 뛰어넘어 담금질의 온도, 유지하는 시간, 식히는 속도 등을 보다 체계화 해 세계가 원하는 고부가 쇳덩이를 내놓는 데는 미흡하다는 것이다.
단조산업은 주물산업과 더불어 모든 산업에 있어서 기초적인 핵심이 되는 산업으로서 고도의 생산기술을 요하는 부분임에도 3D기피 현상으로 인한 기술 및 기능인력의 부족과 생산기술 축적의 부족, 시설부족 등의 이유로 품질의 고급화가 어려운 현실이 안타깝다. (글 : 유상연 -과학칼럼니스트)
불과 10여년 전만 하더라도 조선낫은 벌초를 갈 때면 빠뜨릴 수 없는 연장이었다. 숫돌에 시퍼렇게 날을 간 다음 행여나 다칠세라 새끼줄로 칭칭 동여 맨 뒤 조상님들의 산소를 향해 떠났는데, 낫 한 자루면 모든 것이 해결 가능했다. 풀은 말할 것도 없고 두꺼운 식물이나 작은 나뭇가지도 거침없이 쳐낼 수 있었던 것이다. 기특한 것은 굵고 단단한 나무를 베거나 쳐낼 때 날이 닳아지기는 하더라도 부러지거나 이가 빠지지는 않는다는 것이다.
이런 낫을 만들어 내는 모습도 볼 만했다.
‘싼 값’을 무기로 공장에서 대량으로 찍어내는(주조방식) 왜낫과 달리, 조선낫은 대장간에서 대장장이가 직접 두드려(단조방식) 만들었다. 화덕에서 꺼낸 시뻘건 쇳덩이를 두드리고 물에 담그는 순간 치지직∼쉬이익 소리를 내며 자지러지는 것을 다시 건져내 흥건히 땀방울을 적시면서 쇠망치로 수 백번을 두드리는 대장장이의 손놀림 끝에 조선낫이 탄생한 것이다. 그런데 대장장이들은 단순히 벌겋게 단 쇳덩이를 찬물에 담궈 급랭(急冷)시키고 두드리기만 한 것은 아니었다. 고온에서 급랭하는 담금질을 통해, 보통이면 일어날 변화를 일부 또는 전부 차단하여 필요한 특성만을 나타내게 한 후에는 비교적 저온에서 가열함으로써 담금질로 막았던 변화를 약간 진행시켜 알맞은 특성을 갖게 만드는 ‘뜨임’을 하고, 또 이를 천천히 식힘으로써 금속재료의 뒤틀림을 바로잡거나 상의 변화를 충분히 끝나게 하여 안정상태로 만드는 ‘풀림’ 등을 거치면서 쇳덩이의 성격을 완전히 바꿨다. 이 과정에서 조직을 보다 안정적이고 단단하게 만들기 위해 망치로 쇠를 두드려 주는 것이었다. 도대체 벌겋게 단 쇳덩이를 물에 담그고 두드리면 어떤 변화가 일어나는 것인가?
쇳덩이를 현미경으로 자세히 확대해서 보면 치밀한 금속 조직을 볼 수 있다.
네모, 육각형, 오각형… 모양만 다양한 게 아니라 크기도 제각각인데, 이런 조직들은 온도에 따라 조금씩 다른 특성을 나타내게 된다. 쇳덩이를 급랭시키면 냉각액과 접촉되는 강철의 표면조직은 단단한 마텐자이트가 되고 강철의 내부로 들어갈수록 냉각속도가 늦어져 조직은 질기면서 충격 흡수를 잘하는 펄라이트 조직으로 바뀌게 되는 것이다.
대장장이들은 이처럼 쇳덩이의 성질이 달라진다는 것을 날과 등의 두께를 달리함으로써 경험적으로 알고 있었다. 그들은 쇠의 색깔이 황혼 빛에 이르는 순간을 포착해, 안쪽 날부터 시작해 등 부분까지 순간적으로 물에 담그는 것을 반복했다. 날 부분은 갑작스레 담금질하면 갈라질 수 있기 때문에 손끝에서 나오는 숙련된 기술이 필수적이었다. 이런 과정을 수백 번에 걸쳐 반복하면서, 날 부분은 강하게 만들고 가운데와 등 부분은 약하지만 유연하게 만들었다. 조선낫은 이런 과정을 거쳐 단단한 ‘날’과 낫 날에 가해지는 충격을 흡수하는 ‘등’으로 만들어 졌던 것이다.
오늘날 단조방식으로 금속을 가공하는 원리는 우리 조상들이 사용하는 방식 그대로다.
바이트 ·드릴 ·끌 ·다이스 등 다른 금속재료를 자르거나 깎는 공구의 재료로 쓰이는 강철은 대부분 마텐자이트 조직이 되도록 열처리된다. 자동차 강판이나 항공기 부품 등에는 베이나이트 특성을 갖도록 가공한다. 다만 현대에 와서 달라진 것이라면 대장간에서 쇠를 두드려서 각종 도구들을 만드는 대신, 다이(Die)라고 불리는 아주 단단한 틀 위에 재료를 놓고 자동으로 두드리도록 하는 것이다. 또 급랭할 때 물 대신 기름이나 액체공기 속에 넣는 일도 있고, 찬 공기나 그 밖의 가스를 뿜는 경우도 있다.
그런데 아쉬움이 있다면 현재의 우리 기술수준이 조선낫을 만들던 대장장이의 장인 정신을 뛰어넘어 담금질의 온도, 유지하는 시간, 식히는 속도 등을 보다 체계화 해 세계가 원하는 고부가 쇳덩이를 내놓는 데는 미흡하다는 것이다.
단조산업은 주물산업과 더불어 모든 산업에 있어서 기초적인 핵심이 되는 산업으로서 고도의 생산기술을 요하는 부분임에도 3D기피 현상으로 인한 기술 및 기능인력의 부족과 생산기술 축적의 부족, 시설부족 등의 이유로 품질의 고급화가 어려운 현실이 안타깝다. (글 : 유상연 -과학칼럼니스트)
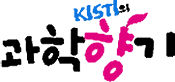
추천 콘텐츠
인기 스토리
-
- [과학향기 Story] '디저트 배'는 진짜였다! 당신 뇌 속의 달콤한 속삭임
- 식사를 마치고 분명히 배가 부른데도, 디저트를 보면 갑자기 내 안의 또 다른 존재가 식욕을 억제하지 못해 꿈틀대기 시작하는 신비롭고 놀라운 경험. 이 꿈 같은 일은 남녀노소 누구에게나 벌어지곤 한다. 이중인격자도 아니오, 어느 슈퍼히어로 영화에서처럼 식탐으로 가득한 외계 빌런을 몸속에 품은 이가 아니더라도 말이다. 그렇다. 두말하면 입 아플 만큼 흔하...
-
- [과학향기 Story] 어디서든 인터넷을 쓸 수 있다…스타링크, 한국 통신 시장 뒤엎나
- 전 지구를 초고속 인터넷 네트워크로 연결하겠다는 일론 머스크의 스타링크가 드디어 국내 서비스를 앞두고 있다. 과학기술정보통신부는 스타링크 서비스의 국경 간 공급 협정 승인을 위한 ‘주파수 이용 조건’을 마련할 계획이라고 밝혔다. 스타링크의 모회사인 스페이스X와 순조롭게 협의가 이뤄지면 다가오는 3월에 국내 서비스를 시작할 수 있다. 과연 스타링크는 국...
-
- 저주파 자극기, 계속 써도 괜찮을까?
- 최근 목이나 어깨, 허리 등에 부착해 사용하는 저주파 자극기가 인기다. 물리치료실이 아니라 가정에서 손쉽게 쓸 수 있도록 작고 가벼울 뿐만 아니라 배터리 충전으로 반나절 넘게 작동한다. 게다가 가격도 저렴하다. SNS를 타고 효과가 좋다는 입소문을 퍼지면서 판매량도 늘고 있다. 저주파 자극기는 전기근육자극(Electrical Muscle Stimu...
이 주제의 다른 글
- [과학향기 for kids] 추위에도 끄떡없어! 북극곰의 털이 얼어붙지 않는 비결은?
- [과학향기 Story] 울퉁불퉁 도로의 포트홀, 해바라기유로 고친다?
- [과학향기 Story] ‘화마’ 불러오는 전기차 화재…피해 심각한 이유는?
- [과학향기 Story] 점점 더워지는 여름, 건물 온도를 낮출 방법은?
- [과학향기 for Kids] 종이에 베이면 왜 이렇게 아플까?
- [과학향기 Story] 영원의 상징 다이아몬드, 실험실에서 만든다?
- ‘누나’가 만들어낸 희소성 만점 핑크 다이아몬드, 비결은 초대륙 충돌
- 2022-2023, ‘양자 개념’이 노벨상 연속으로 차지했다? 양자 연구 톺아보기
- 일장춘몽(一場春夢)이었나? LK-99 초전도체 가능성 ‘0으로 수렴 중’
- 메이드 인 스페이스! 우주에서 약 만드는 시대 온다
아무리 정교한 기계로 만든 것이라 할지라도 인간이 손으로 만든 꼼꼼한 제품은 따라갈수가 없던걸요...
2009-04-07
답글 0
열처리된 대표제품으로 칼을 드시는데..군사잡지에 잘 벼려진 일본도랑 미제기관총탄과의 대결이 있었습니다.워터제트랑도 했구요..트리비아의 샘이란 우리나라 스펀지원조프로그램이었습니다.
7번째 기관총탄에 일본도가 부러지더군요..장인정신과 축적된 아날로그기술이 없이는 불가능한 기술분야가 아닌가 싶습니다.어릴때 쇠부지깽이 마니 달궈서 장난쳤었는데 마르텐사이트조직의 이해를 최근에야 했더랬습니다..
2005-11-08
답글 0
a
2005-11-07
답글 0
a
2005-11-07
답글 0
언제나 우리 조상들의 지혜는 놀랍기만 합니다. 제대로 물려 받지 못한게 아쉬울 따름 입니다.
2005-11-02
답글 0
우리는 말할 것도 없지만 일본도 주물쪽은 인력이 없다더군요... 한국제품 수입해서 쓴다고 들었습니다. 고부가가치 주물은 자기네가 만들지만...
2005-11-02
답글 0
공장에 모터가 많아서 베어링을 자주 교체하는데..
소형 모터에 사용되는 베어링이 국산은 길어봐야 6개월,
일본산은 길면 2-3년이 갑니다..
가격은 일본산이 2배이상 비쌉니다만..
계산상으로 봐도 같은가격의 2배를 견뎌주는 일본산을 어쩔수없이 사용하게끔 되더라구요..
쇠의 열처리에 대한 좋은 내용 감사드려요..
2005-11-02
답글 0